It is recommended that users first read our various REMS presentations prior to viewing this page.
You can read about REMS and view our presentations by clicking here.
1: How can this mining method be patented, and what is to stop me from using some/all of this technology ?
Patents protect inventions which are new, and inventive or innovative. The inventors of the REMS process have invested a significant sum of money during its formulation, the subsequent development of the technology and its technical evaluation, and they have sought to protect this investment through the patent. The process of patenting REMS has involved an exhaustive review which included the rigors of Examination through the Patent’s Office, which the REMS patent has withstood. EMT has sought advice and utilised the services of Cullens Patent and Trade Mark Attorneys right throughout these activities. The resultant patent is now fully enforceable.
2: Will REMS result in more coal loss and dilution?
The top of coal will still be cleaned off by a dozer and then, where required, the coal may be ripped by that dozer, which may even operate under the dragline boom point on occasions as per existing dozer practices. This dozer may or may not be operated as a remote dozer if this particular mine has access to this technology. The dozer will also clean the floor of the pit. The important operational procedure with this sequence is to introduce suitable practices for dragline bucket loading, dis-engagement and thence the carrying of the coal up to the highwall. As this will become a regular activity, it is expected that dragline operators will develop suitable practices which are as good as current coal mining practices.
Some additional dilution might be expected when picking up coal from the highwall stockpile (depending upon what is introduced on the highwall in this regard), and this has been factored into the cost analysis as an additional CHPP processing cost in the financial modelling that external advisors have developed.
3: Can REMS be used if there are 2 coal seams separated by an Interburden or Partings layer?
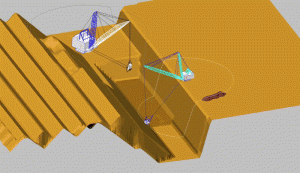
Diagram illustrating a second machine on the highwall to remove coal and/or partings. CLICK TO ENLARGE
For thin waste partings that can be ripped by a dozer, the introduction of the REMS process would be readily manageable, but would introduce an additional mining process impacting on dragline time allocation. However for thicker waste partings of greater than approx. 3 metres (and which may require drill and blast activities), REMS would be more difficult to implement in it’s simplest form - but not impossible. It is recommended that a more detailed investigation of the particular coal resource geology and the possible introductory feasibility of the REMS process be investigated in this instance.
As a part of the solution for 2 coal seam mining by the REMS process, or for the potential split seam mining to take advantage of differential coal quality in some part of coal seams, a separate coal loading machine located on the highwall could be used (refer the diagram herein). This could take the form of a modified dragline or a crane. This approach separates the operation of waste overburden removal from that of the coal excavation and elevation activity, thereby allowing the handling of multi pass operations for coal loading and partings removal.
4: How is product coal quality managed when there is no selective mining from the pit and in-pit coal inventory is minimal?
In-pit coal inventory is reduced substantially, as are other inventories (drilling, blasting, pre-stripped overburden etc) so that a smaller operating footprint can be utilised for the active mining area. Consequently, to manage coal preparation plant feed sources, raw coal stocks will need to be managed from stockpile – ie. either on the highwall, or at the ROM adjacent the preparation plant. This may require a change to current operating practices to take advantage of the substantial financial benefit of not having large in-pit stocks available to mine as required.
5: What changes are required with different draglines?
Larger draglines with different boom angles/lengths and operating envelopes will have a different optimal geometric pit design – for example an increase of 5 metres in possible dig depth and reach may allow a slightly wider pit, and/or an increased highwall.
6: What is the implementation plan to support the introduction of REMS at a minesite?
EMT is interested in licencing the technology to mining operators/mine owners, and to provide support to the initial evaluation and introduction of REMS via a consulting service. This consulting service would utilise the independent technical experts and advisors who have been involved with the development and technical evaluation of REMS, as they are familiar with the technology already. Having been involved with the independent review and evaluation processes, they are ideally positioned to assist mine operators/owners with their own evaluation exercises. This consulting service will be managed by Geoff Sengstock and Jeff Berndt, who are experienced mining consultants, and who also have access to Bill McKinstrey for operational expertise. They can each be contacted separately or via EMT.
7: When introduced to an existing mine site, what impact could REMS have over the next few strips, and could this help me weather the current low coal prices?
The introduction of REMS to an existing mine site with existing ramp voids and wide strip voids will result in significant additional benefits over the next few strips as these voids represent a large opportunity. These benefits are in addition to the claimed benefits of EMT over and above current mining methods, and should result, amongst other outcomes, in a fundamental reduction in costs. This arises from the combination of the following major factors:
- additional casting of blasted overburden material in sequentially reducing strip widths from say 60m to 50m to 40m;
- ramp voids to be filled with pre-stripped waste, with shorter haul distances and by not having to haul up long ramps to dump spoil;
- low dragline dumps during the transition from wide to narrow strips eg. 60m to 50m to 40m, etc;
- additional dragline productivity though reduced positioning time on bench, reduced swing angles, no rehandled waste in pit, and reduced hoist time.
8: Are there any particular changes required to be made to Drill and Blast practices if REMS is introduced?
Where REMS is introduced, cast blast designs applicable to narrower strips will likely result in an increase in the average powder factor (from the geometry change in blast designs) and that may increase the explosives quantities and accessories that are required.
Otherwise, normal good blast practices for presplit and waste blasting will be required, with control of coal damage and movement to be well-managed. The dragline will be able to dump waste against the coal edge for coal buffering.